Plasma Monitoring with Modular, High-resolution Spectroscopy 海洋電漿測量
原文網址:https://www.oceaninsight.com/blog/plasma-monitoring/?utm_campaign A high-resolution spectrometer monitored changes in argon emission after different gases were added to a closed-reaction plasma chamber. Plasma characteristics derived from these me
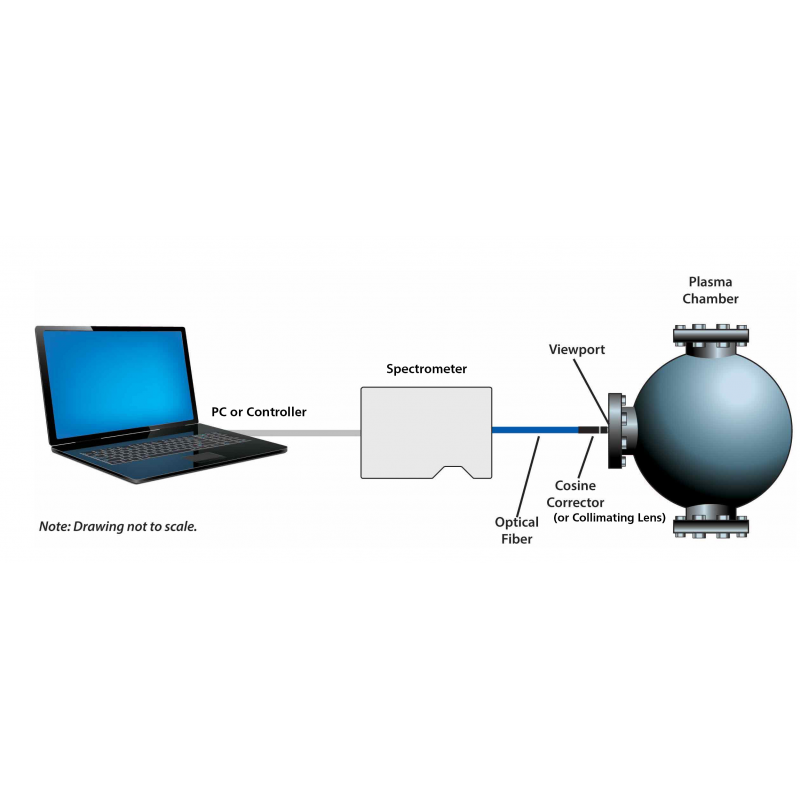
- 產品說明 (點擊展開觀看)
-
A high-resolution spectrometer monitored changes in argon emission after different gases were added to a closed-reaction plasma chamber. Plasma characteristics derived from these measurements can be used for monitoring plasma processes.
Background
Plasma is an energized, gas-like state where a fraction of the atoms has been excited or ionized to form free electrons and ions. As the electrons of excited neutrals return to the ground state, the plasma emits light at wavelengths specific to the atoms present in the plasma. The spectral profile of the emitted light is used to determine the composition of the plasma. Plasma is formed using a range of high energy methods to ionize the atoms including heat, high powered lasers, microwaves, electricity and radio frequency.
Plasma is used in industries including semiconductor manufacturing for applications including elemental analysis, film deposition, plasma etching and surface cleaning. Precise monitoring of plasma-based processes can help to minimize wafer contamination, improve quality and optimize production yields.
Plasma Monitoring
Plasma monitoring via the emission spectrum measured for the plasma sample can provide detailed elemental analysis and determination of critical plasma parameters required for controlling a plasma-based process. The wavelengths of the emission lines identify the elements present in the plasma, with emission line intensity used to quantify particle and electron densities in real time for process control.
Parameters including gas mixture, plasma temperature and particle density are critical for controlling the plasma process. Changes to these parameters via introduction of various gases or particles to the plasma chamber will change the plasma characteristics, impacting the plasma-substrate interaction. The ability to monitor and control the plasma in real time leads to improved processes and outcomes.
For example, plasma monitoring is important for process control in plasma-based etching processes. In the semiconductor industry, wafers are fabricated and manipulated using lithography techniques. Etching is a major part of this process in which materials can be layered to a very specific thickness. As the layers are etched on the wafer surface, plasma monitoring is used to follow the etching through the wafer layers and determine when the plasma has completely etched a specific layer and reached the next. By monitoring the emission lines generated by the plasma during etching, the etching process can be followed precisely. This endpoint detection is critical to the production of semiconductor materials using plasma-based etching processes.
Plasma Monitoring Setups
Plasma monitoring can be managed with a flexible, modular setup using a high-resolution spectrometer like the HR series or Maya2000 Pro from Ocean Insight (the latter is a popular option for UV gases). For a modular setup, an HR spectrometer can be combined with solarization-resistant optical fiber to acquire qualitative emission data from plasma formed in a chamber. If quantitative measurements are required, users can add a third-party spectral library against which to compare data and quickly identify unknown emission lines, peaks and bands.
An important consideration when monitoring plasma formed in a vacuum chamber is the interface to the chamber. Instrument components can be introduced into a vacuum chamber or set up to view the plasma through a viewport. Vacuum feedthrough assemblies or custom fibers designed to withstand the harsh conditions in the chamber can be used to couple components into the plasma chamber.
For monitoring the plasma through a viewport, a sampling accessory like a cosine corrector or collimating lens may be required depending on the size of the plasma field to be measured. With no sampling accessory, the distance from the fiber to the plasma will dictate the imaged area. Use a collimating lens for a more localized collection area, or a cosine corrector for light collection over a 180° field of view.
Measurement Conditions
An HR series high resolution spectrometer was used to measure changes in the emission for argon plasma as other gases were introduced to a plasma chamber. Spectral data were acquired for the plasma contained in a closed reaction chamber with the spectrometer, fiber and cosine corrector collecting emission spectra through a small window outside the chamber (Figure 1).
Figure 1: A modular spectrometer setup can be configured for plasma measurement in a vacuum chamber.
An HR2000+ high resolution spectrometer (~1.1 nm FWHM optical resolution) configured to measure emission from 200-1100 nm (Grating HC-1, SLIT-25) was coupled to a cosine corrector (CC-3-UV) using a solarization-resistant fiber (QP400-1-SR-BX fiber). A CC-3-UV cosine corrector sampling accessory was chosen to acquire data from the plasma chamber and to address differences in plasma intensities and inhomogeneous fouling of the measurement window. Other sampling options include collimating lenses and vacuum feedthroughs.
Results
The spectrum measured for argon plasma through the window of the plasma chamber is shown in Figure 2. The strong spectral lines from 690-900 nm are emission lines from neutral argon (Ar I) with the lower intensity lines from 400-650 nm resulting from the singly ionized argon atoms (Ar II). The emission spectrum shown in Figure 2 is a great example of the rich spectral data measured for plasma emission. This spectral information can be used to determine a range of critical parameters for monitoring and controlling a plasma-based process during semiconductor fabrication.
Figure 2: Emission of argon plasma is measured through a vacuum chamber window.
Hydrogen gas is a secondary gas that can be added to argon plasma to change its properties. In Figure 3, the effect of adding hydrogen gas to argon plasma is shown as increasing concentrations of hydrogen gas are added to the chamber. The ability of the hydrogen gas to change the characteristics of the argon plasma is clearly shown by a decrease in the intensity of the argon lines between 700-900 nm while the increasing concentration of hydrogen gas is reflected in the appearance of hydrogen lines between 350-450 nm. These spectra demonstrate the power of measuring plasma emission in real time to assess the impact of a secondary gas on plasma properties. The spectral changes observed could be used to ensure optimal amounts of secondary gases are added to the chamber to achieve the desired plasma characteristics.
Figure 3: Adding hydrogen gas to the argon plasma changes its spectral properties.
In Figures 4-5, emission spectra measured for the plasma before and after the addition of sheath gas to the chamber are shown. Sheath gas is used to decrease contact between the sample injector and the sample to reduce problems due to sample deposition and carryover. In Figure 4, the argon plasma emission spectrum is shown before the addition of sheath gas. The emission spectrum measured after sheath gas addition is shown in Figure 5. The addition of sheath gas leads to changes in the argon emission spectrum as seen in the loss of the broad spectral lines just below 400 nm and at ~520 nm.
Figure 4: Argon plasma emission is measured in the vacuum chamber before the addition of sheath gas.
Figure 5: With the addition of sheath gas, argon emission characteristics are noticeably different below 400 nm and at ~520 nm.
Conclusion
UV-Vis-NIR spectroscopy is a powerful method for measuring plasma emission to enable elemental analysis and precise control of plasma-based processes. The data shown here illustrate the power of the modular spectroscopy approach for plasma monitoring. The HR2000+ high resolution spectrometer and modular spectroscopy approach worked well to measure plasma emission spectra through the window of a plasma chamber as chamber conditions were adjusted.
Additional plasma monitoring options are available, including the Maya2000 Pro, which has excellent response in the UV. Also, spectrometers and subsystems can be integrated into other devices and combined with machine learning tools for even more sophisticated control of plasma chamber conditions.
Download a complete version of this application note as a PDF.